1. Introduzione
Tecnologia della saldatura Laser ha rivoluzionato i processi di fabbricazione di vari settori, con impareggiabile precisione, velocità e versatilità. Tuttavia, il costo del laser, impianti di saldatura diventa spesso un fattore critico nel processo decisionale per le imprese, in considerazione di questo investimento.
In questa guida completa, esploreremo:
- Mappa guasti del laser saldatore prezzi per tipologia e capacità
- Analisi approfondita dei fattori che influenzano la saldatura laser costi della macchina
- Esempi del mondo reale del costo totale di proprietà calcoli
- I consigli dell'esperto per l'ottimizzazione del laser di saldatura investimento
Se sei un piccolo laboratorio di proprietario o di un grande impianto di produzione di manager, questa guida vi aiuterà a navigare il complesso di paesaggio di saldatura laser macchina di spese.
2. Tipi di Laser, Macchine per la Saldatura e il Loro Prezzo Varia
a) Laser Palmare Saldatore Prezzo
- Gamma: $4,700 – $26,300
- Modelli popolari:
- Entry-level (1000W): $5,000 – $8,000
- Mid-range (1500W): $10,000 – $15,000
- High-end (2000W+): $18,000 – $26,300
- Adatto per: Piccole officine, riparazioni in loco, creazione di gioielli
- Principali vantaggi: Portabilità, facilità d'uso, basso investimento iniziale
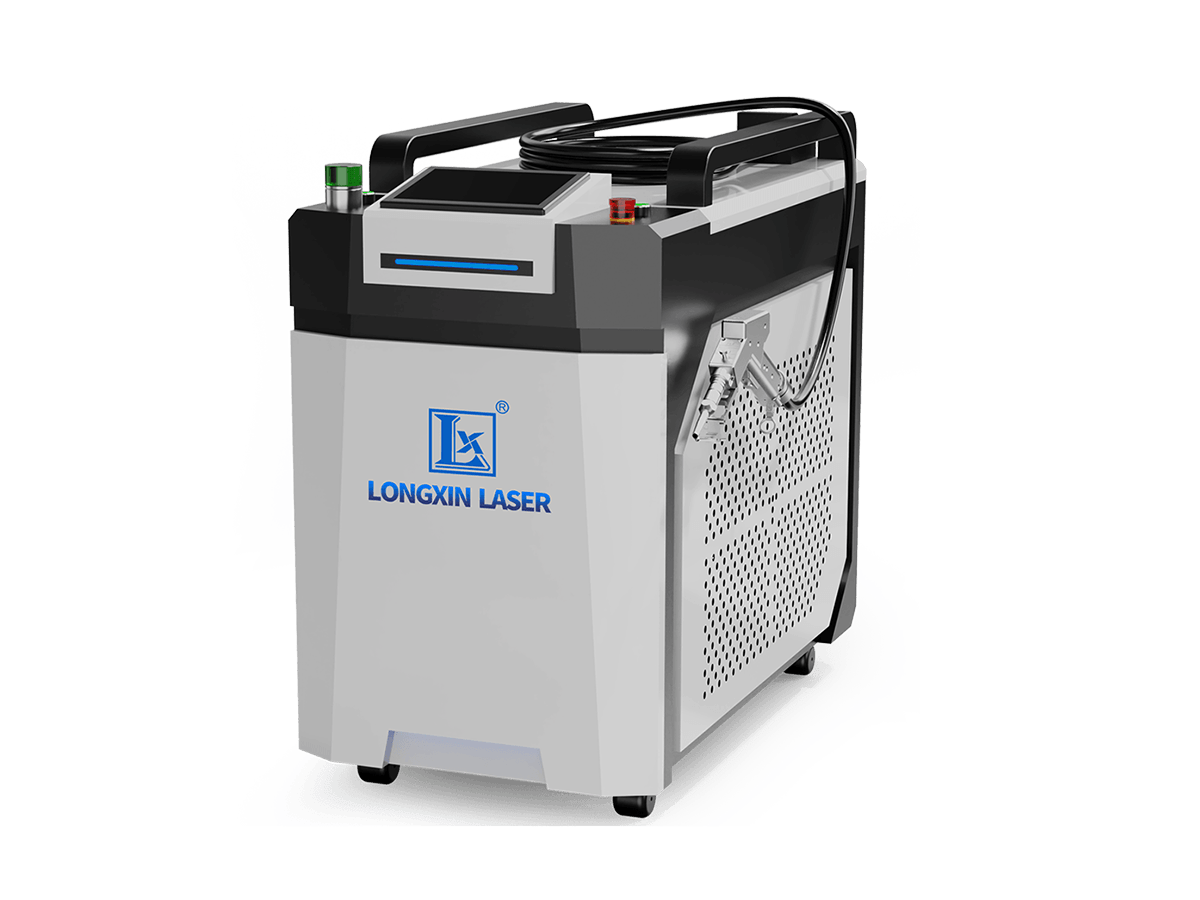
b) Laser CNC, Macchina di Saldatura Prezzi
- Gamma: $30,000 – $150,000+
- Ripartizione dei prezzi da parte del potere:
- 300W – 500W: $30,000 – $50,000
- 600W – 1000W: $50,000 – $80,000
- 1000W – 2000W: $80,000 – $150,000+
- Adatto per: Medie e grandi imprese manifatturiere, della produzione di componenti automobilistici
- Vantaggi chiave: Alta precisione, capacità di automazione, coerente della qualità della saldatura
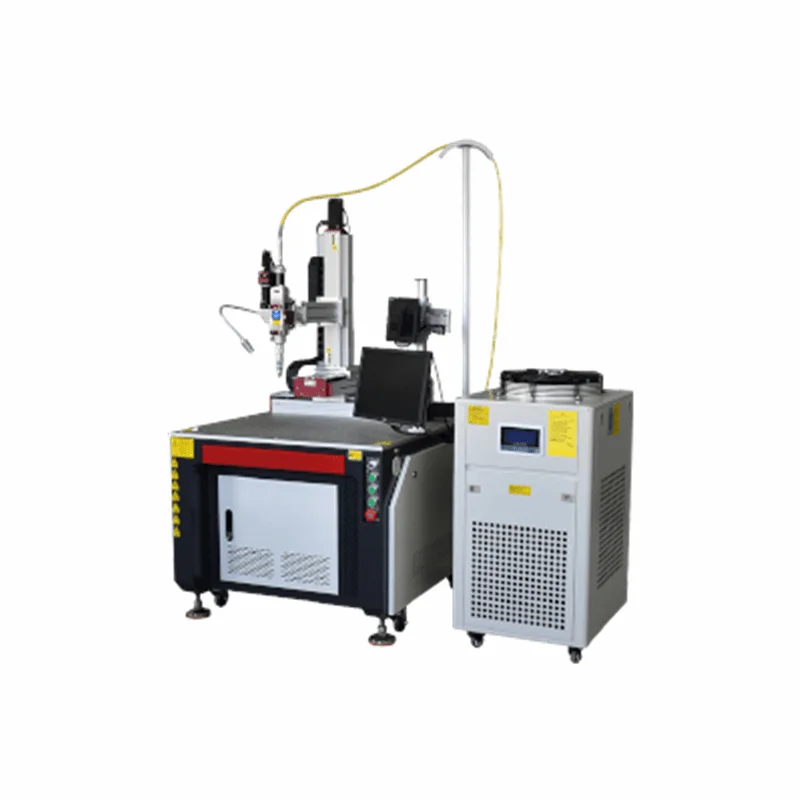
c) impianti di Saldatura Laser Robot Spese
- Gamma: $100,000 – $500,000+
- Fattori di costo:
- Braccio Robot raggiungere e capacità di carico
- Sorgente Laser di potenza (in genere 2000W – 6000W)
- Complessità di integrazione e di programmazione personalizzata
- Adatto per: produzione su Larga scala, linee di assemblaggio per automotive, aerospaziale industria
- Vantaggi chiave: il più Alto livello di automazione, 3D saldatura di capacità di integrazione con le linee di produzione
d) Combinazione di taglio Laser e Prezzi Saldatore
- Gamma: $50,000 – $200,000
- Variazioni di prezzo:
- I modelli di base (500W – 1000W): $50,000 – $80,000
- Modelli avanzati (1000W – 2000W): $80,000 – $150,000
- Sistemi di fascia alta (2000W+): $150,000 – $200,000+
- Adatto per: Lavoro negozi, servizi di prototipazione, versatile operazioni di produzione
- Vantaggi chiave: Multi-funzionalità, risparmio di spazio, costo-efficace per le aziende che necessitano di taglio e saldatura

3. Fattori Che Influenzano La Saldatura Laser Costi Della Macchina
a) Potere del Laser
- Impatto sul prezzo: 15% – 30% di aumento di potenza per il raddoppio
- Esempio: 1000W sistema potrebbe costare $50,000mentre un 2000W sistema potrebbe essere $65,000 – $75,000
- Considerazioni: l'incremento di potenza è più veloce velocità di saldatura e materiali di spessore
b) la Precisione e la Qualità del Fascio
- Di alta precisione, sistemi può costare il 20% – 40% in più rispetto ai modelli standard
- Fascio fattori di qualità:
- Fascio Parametro del Prodotto (BPP): limite Inferiore di BPP = Maggiore qualità = costo più elevato
- M2 valore: più Vicino a 1 = Migliore qualità = Più costoso
c) Funzioni di Automazione
- Di base di controllo CNC: Incluso nel prezzo base
- Funzioni avanzate di ripartizione dei costi:
- Cambio utensile automatico: $5,000 – $15,000
- Sistemi di visione per la saldatura di tracking: $10,000 – $30,000
- Integrata sistemi di controllo di qualità: $20,000 – $50,000
d) la Reputazione del Marchio e di Assistenza post-Vendita
- I marchi Premium possono ricaricare il 10% – 25% più di meno noti produttori
- Fattori da considerare:
- Durata della garanzia e copertura
- Disponibilità di locali tecnici di servizio
- Costo e la disponibilità di parti di ricambio
e) Caratteristiche Aggiuntive
- Specializzata teste di saldatura: $5,000 – $20,000 a seconda della complessità
- Avanzati sistemi di raffreddamento: $3,000 – $10,000
- Aspirazione fumi: $2,000 – $8,000
- Software per la saldatura di design pattern: $2,000 – $15.000 per ogni licenza
4. Capire il Costo Totale di Proprietà per la Saldatura Laser Macchine
a) in Corso, le Spese di gestione
- Consumo di energia:
- Costo medio per ora: $1.50 a $3,00 per un 1000W sistema
- Costo annuale (2000 ore di funzionamento): da $3.000 – 6.000 dollari
- Materiali di consumo:
- Gas di protezione: $500 – $2.000 all'anno
- Parti di ricambio (ugelli, lenti): $1,000 – $5.000 per anno
- Manutenzione:
- Manutenzione ordinaria: 2% – 5% del costo del macchinario all'anno
- Esempio: $50,000 macchina = $1,000 – $2,500 costo annuo di manutenzione
b) la Formazione e i Costi di Manodopera
- Operatore iniziale di formazione: $2,000 – $5.000 per operatore
- Formazione avanzata per tecnici: $5,000 – $10.000 per persona
- Potenziale aumento di stipendio per operatori specializzati: 10% – 20%
c) Ammortamento e il Valore di Rivendita
- Tipico tasso di ammortamento: 15% – 20% all'anno per i primi 5 anni
- Esempio: $100,000 macchina potrebbe essere la pena di $40.000 – 50.000 dollari dopo 5 anni
- Fattori che influenzano il valore di rivendita:
- La reputazione del marchio
- Storia della manutenzione
- I progressi tecnologici in modelli più recenti
5. Confronto dei costi di: Saldatura a Laser, rispetto ai Tradizionali Metodi di Saldatura
a) Investimento Iniziale
- La saldatura Laser: $30.000 a $500,000+
- Di saldatura tradizionali (ad esempio, TIG, MIG):
- Configurazione di base: $2,000 – $5,000
- Sistemi avanzati: $10,000 – $50,000
b) Costi Operativi (base 2000 ore annuali di funzionamento)
- La saldatura Laser:
- Energia: $3,000 – $6,000
- Materiali di consumo: per $1500 – $7,000
- Manutenzione: $1,000 – $25,000 (a seconda della macchina di costo)
- Di saldatura tradizionali:
- Energia: $1,000 – $3,000
- Materiali di consumo (elettrodi, fili): $5,000 – $15,000
- Manutenzione: $500 – $2,500
c) a Lungo termine ROI Fattori
- Aumento della produttività con la saldatura a laser: 30% – 50% in molte applicazioni
- Risparmio di materiale: Fino al 20% di riduzione di sprechi di materiale
- Il miglioramento della qualità: il Potenziale di riduzione del 50% delle rilavorazioni e scarti
6. Consigli per Budget-Friendly Laser Saldatore Acquisti
a) Esplorare Usati e Ricondizionati Opzioni
- Il potenziale di risparmio: 30% – 50% off prezzo originale
- Chiave controlli prima dell'acquisto:
- Ore di esercizio
- I registri di manutenzione
- Rimanenti laser sorgente di vita
b) Opzioni di Leasing e Finanziamento
- Tipiche condizioni di locazione: 3-5 anni
- Pagamenti mensili: Spesso 2% – 3% del totale del costo del macchinario
- Vantaggi:
- Iniziale inferiore esborso di denaro
- Potenziali vantaggi fiscali
- Più facile aggiornamenti alle nuove tecnologie
c) Borse di studio e Incentivi
- I programmi di governo: Può coprire il 10% – 30% del costo del
- Efficienza energetica sconti: Potenziale di $5.000 – 20.000 dollari di risparmio
- La ricerca e lo sviluppo di crediti di imposta: Fino al 20% della qualificazione di spese di
7. Future Tendenze del Laser, Macchina di Saldatura Prezzi
a) i Progressi Tecnologici
- Laser a fibra miglioramenti: il Potenziale del 5% – 10% riduzione dei costi per anno
- Una maggiore efficienza energetica: si Possono ridurre i costi operativi dal 10% al 20%
b) la Concorrenza del Mercato
- I nuovi operatori provenienti dai mercati emergenti: Potrebbe portare a un calo dei prezzi del 10% – 15%
- Consolidamento tra giocatori affermati: Potrebbe stabilizzarsi o aumentare leggermente i prezzi
c) Tecnologie Emergenti
- AI-assistita di saldatura: Potenziale di $10.000 – 50.000 $di costo dell'add-on
- Laser verde tecnologia: Può aumentare i costi iniziali del 20% – 30%, ma anche di offrire a lungo termine il risparmio energetico
Tenuto conto di questi dettagliate fattori e sfruttando i consigli, le aziende possono prendere decisioni informate circa l'investimento in tecnologia della saldatura laser, bilanciare i costi con i benefici potenziali per trovare la soluzione più conveniente per le loro esigenze specifiche.